Graphene
2023.04.26 14:45
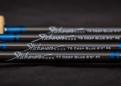
Yes or no?
Lately we have been often asked wether we plan to use graphene in our blanks any time soon. Alejandro Viñuales, the engineer behind our blanks (who happens to be one of the best fly casters in the world) has nearly 20 years of experience in testing new materials and their combinations for manufacturing fly rods, so he is probably to most qualified person to answer this question. Here are his thoughts on the topic:
Before talking about the possibilities of graphene or carbon nanotubes in fiber-resin compounds, it's good to understand these materials, their qualities and how they might improve the end product.
Graphene and nanotubes, like carbon fiber, are made up of carbon molecules with hexagonal structure.
In nature, the usual presentation of graphene is in the form of graphite, which is essentially nothing more than a large number of neatly stacked graphene layers with a crystalline structure that makes the cohesion between the layers very weak. When we write with a graphite pencil, the mark it leaves on the paper is nothing but graphene particles falling off the graphite. This graphite characteristic was taken advantage of to get enough graphene for experimenting for the first time, using a simple duct tape to separate the outer layer from the rest of the layers of a graphite block and subsequently dissolving the duct tape. Commercial graphene is currently obtained through more complex, but also more efficient systems. A layer of graphene is as thick as an atom, it’s practically two-dimensional, and if we’re talking about nanographene at least one side of the particle should be less than 100 nanometers long.
If we imagine graphene as a chicken coop’s classic hexagonal mesh, carbon nanotubes would be the same mesh rolled up forming a thin hollow cylinder. Nanotubes often grow on top of themselves, forming multiple-wall nanotubes whose mechanical characteristics are still debated whether they are better or worse than single-wall ones, which some call graphene nanotubes.
A nanotube has a diameter of approximately one nanometer, one millionth of a millimeter, which is about 5,000 times finer than latest-generation carbon fiber, whose diameter is very close to 5 microns (earlier carbon fibers were somewhat thicker).
Carbon fiber is also formed by graphene layers, or rather graphene tapes. Unlike in graphite, these ribbons are grouped without crystal clear order, with a turbostratic structure more or less complete depending on the type of fiber. This makes the cohesion of graphene mesh much greater in carbon fiber than in graphite, and makes carbon fiber the reinforcement material with the largest elastic module we can currently use in a fiber-resin compound.
The above statement may sound strange if we know that nanotubes have an elastic module that at least doubles that of high-module carbon fibers and a resistance that could be up to ten times higher (keep in mind that the mechanical characteristics of carbon nanocompounds are usually obtained using mathematical models, in practice the numbers can vary greatly because molecular structures are not always perfect). This being true, the problem is currently a viable system to use nanotubes or nano graphene as a base booster or as fiber of a composite material that would allow us to use it as a substitute for carbon fiber.
When nanotubes were discovered, in the early 90s, I expected it wouldn't take long to have carbon-like nanotubes but much thinner, making lighter and more durable rods than today. Unfortunately, although ten years have passed and nanotubes of more than half a meter long were obtained (with very interesting electrical conductivity qualities) the current cluster nanotubes fiber that we find on the market are far from achieving the theoretical mechanical qualities of an isolated nanotube. The elastic module of these fibers does not currently reach even one tenth of a standard HM carbon fiber.
The obvious alternative and theoretically much simpler, is to take advantage of the mechanical qualities of these materials is the use as dopants (additives) in the resins of carbon fiber compounds. That is, not to use nanocarbon as a composite reinforcement but to improve the mechanical qualities of the matrix (resin). This is nothing new and has been done many times in the past with other materials, for example with silica nanopheres, nanofibrilles (nanowhiskers) or metallic nanoparticles in the case of fly rods with very inconclusive and rather disappointing results.
There are a couple problems with adding dopants in resin.
On the one hand, although the role of resin in aspects such as rigidity or resistance of a rod is fundamental, in percentage terms it is very low. Major improvement in the elastic module or resistance module of the resin means very little improvement on the elastic module or strength module of the compound, less the higher the fiber module applied.
On the other hand, incorporating particles with mechanical characteristics extremely different from those of the matrix in the resin runs the risk of disrupting, by agglomerations, the stability of the compound. This puts a limit on the amount of dopant we can incorporate into resin without degrading its qualities, and thus puts a limit on the improvements we can achieve in those resins with the simple system of adding a dopant.
In the article “Recent Developments in Graphene Oxide/Epoxy Carbon Fiber-Reinforced Composites”, published in “Frontiers in Materials” three years ago, we can read: “simple mixing of graphene based nanofiller with epoxy is not a viable method for improving matrix properties due to challenges of achieving a homogeneous dispersion”.
Does this mean nanocarbon can't help us improve our rods? Not at all, it means it hasn't been commercially done yet. No one currently produces a "nanocarbon" epoxy resin that undoubtedly improves, in practice, the structural qualities that a fly rod requires and which offer us the most advanced resins on the market. A simple fact: No carbon fiber manufacturer (Toray, Mitshubitshi, Toyo Tenax, and Hexcel) uses resin with nanographene or nanotubes for their high-performance prepregs.
Sure there are a few small companies in countries not susceptible to misleading advertising that offer prepreg with nanographene, which supposedly enhances their mechanical qualities, for example Haydale in UK. We can download on their website the data of the "mechanically enhanced prepreg", code GA-MEC, which uses Toray T800 fiber and nanocharged resin: voltage resistance 2040.8 MPa; elastic module 151.8 GPa. If we compare this with the standard Toray prepreg for the same fiber: voltage resistance 3290 MPa; 163 GPa elastic module.
While I acknowledge that the comparison isn’t perfect, because both manufacturers use different systems of evaluation, it is obvious that this huge improvement in mechanical qualities is not reflected in the data.
In 2011, the company Antolín launched a graphene and carbon nanofiber production plant in Burgos. I think I was one of the first to be interested in their product, and obtained a generous sample of nanographene with which I could conduct quite a bit of testing. What I didn't get was finding a way to improve my blanks with this material but I did find other applications for it. Time spent in those tests taught me to be prudent and distinguish the possibilities from the realities.
The above doesn’t mean I don’t seek to stay up-to-date on composite technology, or that I don’t follow the latest research in materials that could one day reach our rods. For example GO, graphene oxide (graphene with oxygen atoms and added hydroxyl groups, which increase both their stability and their ability to react and bind to other materials), is very promising and could help solve the problem of adhesion between fiber and resin, but not by simply adding GO to the resin, something that would be worth little by itself, however incorporating it utilising different methods that are still being researched, to the surface of carbon fiber could greatly improve the adhesion between the booster and the matrix and could also allow the addition of nanoparticles in the resin to have a greater effect on the compound. This could mean a major qualitative leap in the future of composites, but we'll still have to wait a few years to see it.